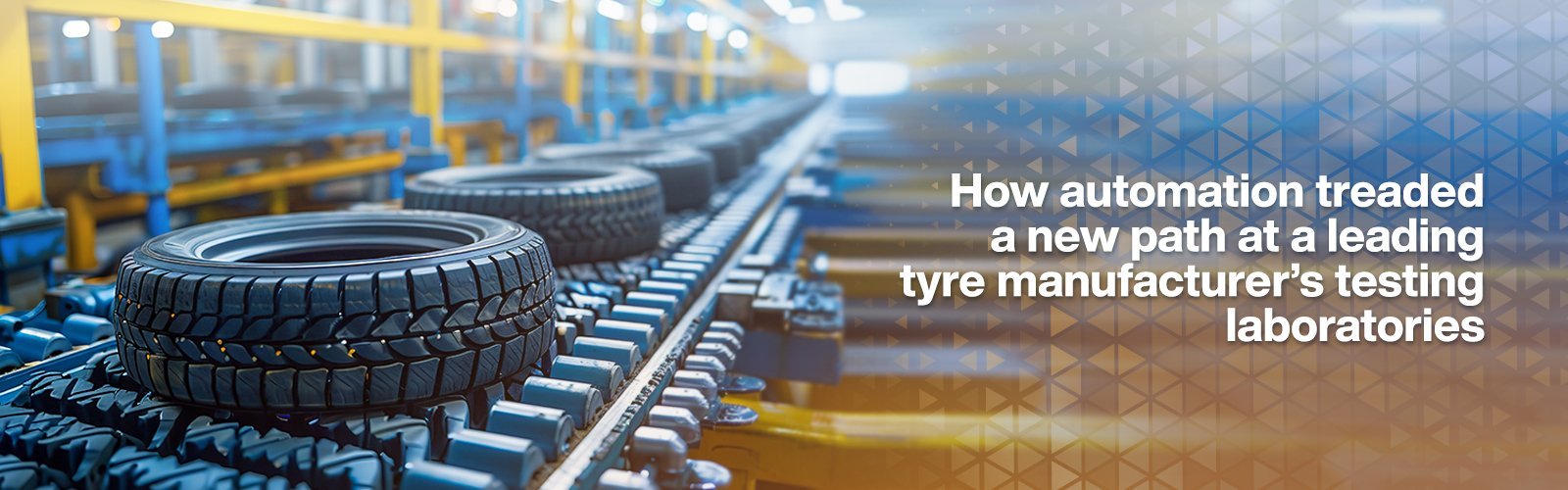
How automation treaded a new path at a leading tyre manufacturer’s testing laboratories
One of our prominent clients, a global leader in tyre manufacturing, produces over 165 million tyres annually. Each tyre undergoes rigorous testing at their plant in Halol, Gujarat, to ensure quality and safety. However, managing such a vast operation was challenging due to outdated processes.
‘We have been able to refine the documentation process for much quicker turnaround time. What used to take a few weeks, now just requires a few hours.’ – Sr. Manager of R&D and testing Division.
Running in circles
The organization operations run at a very large scale, thus managing all resources at the same time was proving to be a challenge. Some of the challenges experienced by the key stakeholders are;
- Managing 100+ critical devices in production and R&D.
- Lack of real-time visibility for device status and failures.
- Vendor accountability for timely maintenance.
- Managing historical data, calibration records, and test results manually.
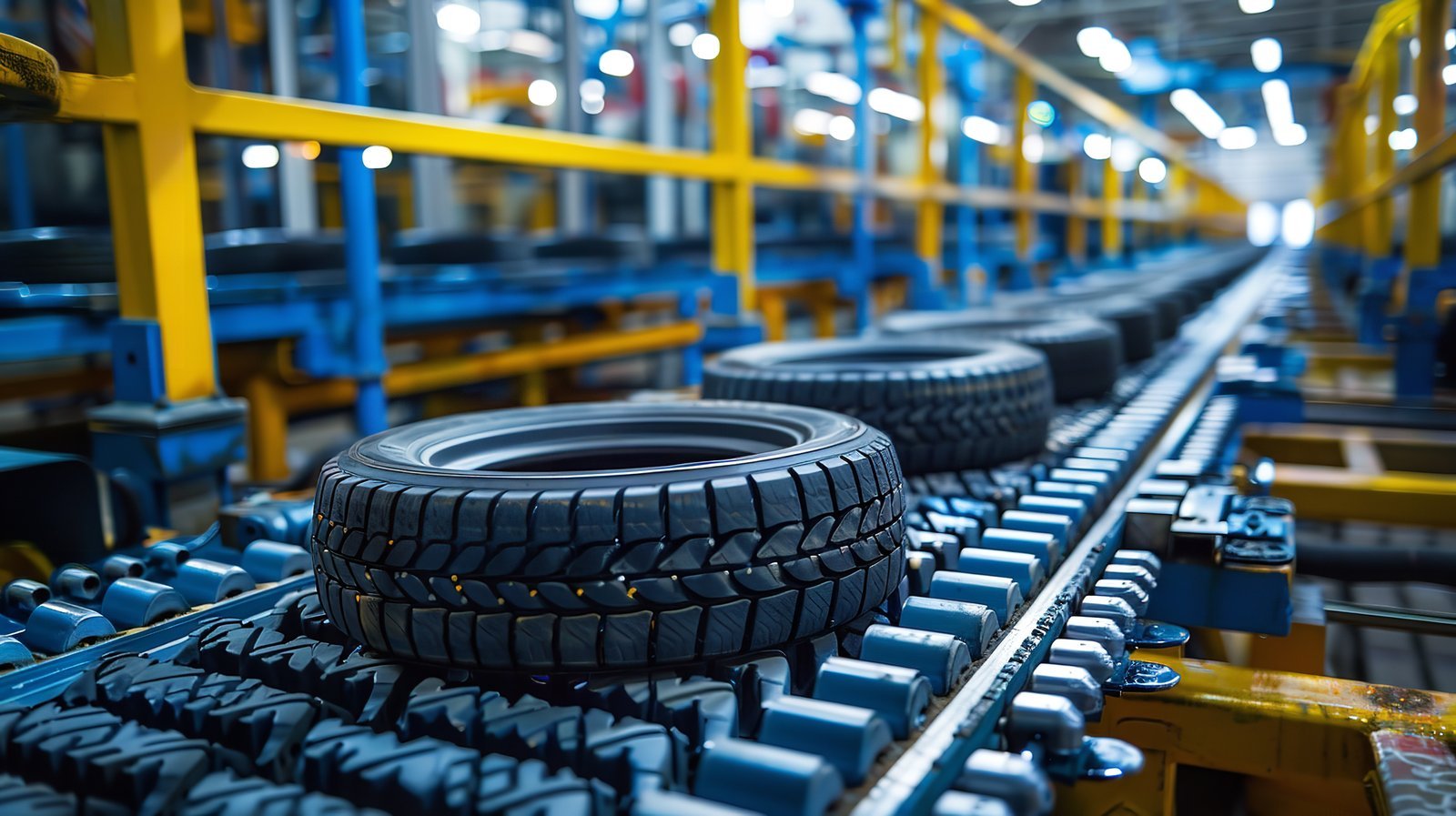
Rolling out Industry 4.0
After spending a considerable time decoding the requirements from various stakeholders and key persons within the processes, we were able to provide a tailored solution for their needs.
- After detailed understanding of the client’s pain points and the elaborate operations procedure, our team was able to work on a customized solution to help cater to their needs.
- Inventory management automation and AMC software for efficient resource allocation.
- Digital integration with all testing equipment, capturing real-time data.
- Predictive analysis using machine learning to forecast maintenance needs.
- SAP integration for automated purchase orders for spare parts.
- Auto-scheduling of maintenance activities based on predictive insights.
- Monitoring the time of loading and unloading of vehicles to ensure efficiency.
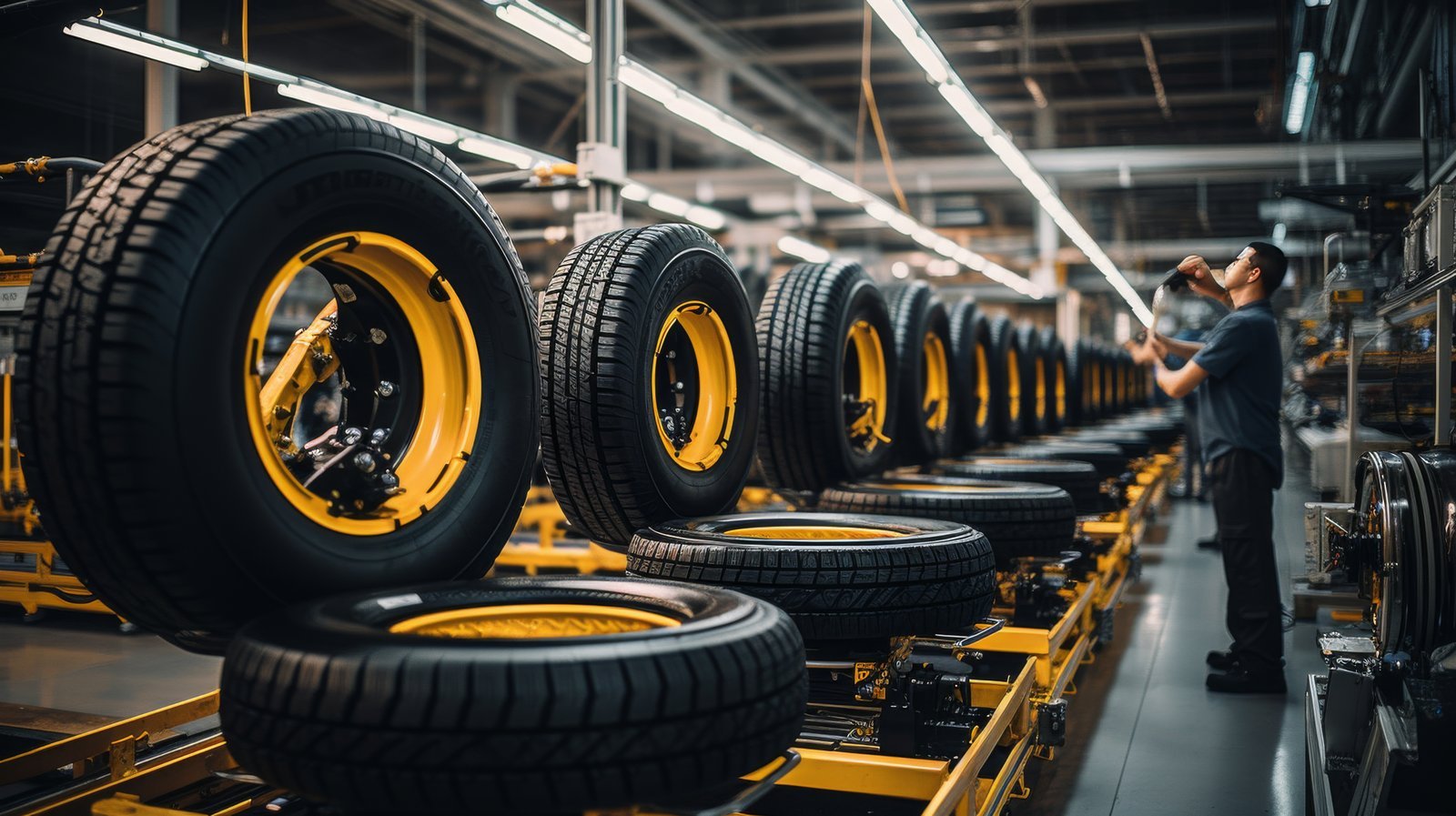
Traction boosting results
As soon as the implementation was completed, results were starting to show in terms of data management, turn around times, and more.
- Quick adoption by over 40 team members, thanks to a customized workflow.
- Improved turnaround time for spare part replenishment and operational efficiency.
- Standardization across processes, ensuring consistency and quality.
- Faster access to historical data for trend analysis, enabling better decision-making.
- Predictive maintenance forecasting ensured smooth operations, minimizing downtime.
- Through automation, the company significantly improved regulatory compliance, process efficiency, and overall digitalization of its testing facilities.
- This success has now been expanded to other departments, driving further efficiencies in the broader operations.